RailVision AI
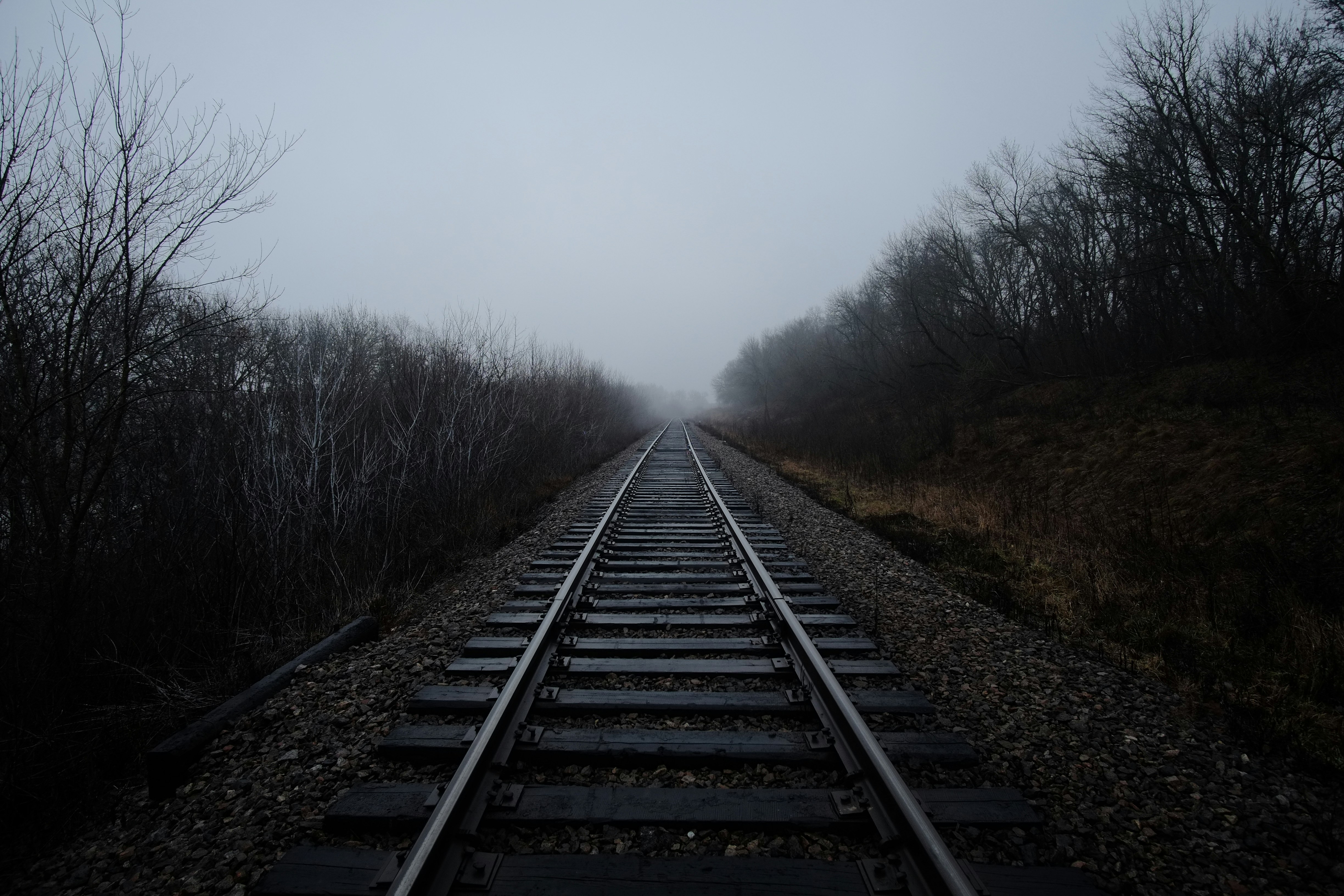
Contamination from railway ballast represents a critical challenge for railway infrastructure maintenance companies. This problem directly affects the stability and safety of railways, increasing operational risks and maintenance costs. Traditional manual inspections are not only slow and expensive, but they are also prone to diagnostic errors, making it difficult to accurately identify the contamination and its depth. In addition, the interpretation of data generated by technologies such as GeoRadar 3D adds complexity, since these are large volumes of information that are difficult to process using conventional methods. Therefore, companies need a solution capable of accurately identifying contamination patterns, determining their depth and optimizing maintenance strategies, reducing both costs and intervention times.
To address this problem, we developed an advanced analysis model based on 3D-GeoRadar data, specifically designed to detect pollution patterns in railway ballast and accurately calculate its depth. The system begins with detailed data processing, filtering noise and extracting key features from the GeoRadar 3D signals. On this basis, we implemented a deep learning architecture using PyTorch, which allowed us to accurately analyze the patterns underlying the data and provide reliable estimates of the location and depth of the contamination. The solution was deployed in a robust environment using MLFlow and Docker, ensuring its reproducibility and scalability. In addition, Apache Airflow was integrated for the automated orchestration of data flows, allowing for efficient and continuous analysis. This innovative approach not only makes it easier to detect pollution, but it also transforms large volumes of data into actionable information, optimizing railway maintenance.
The development of this system has meant a significant change in the management of railway maintenance. On the one hand, the accuracy in detecting contamination has dramatically improved, reaching levels above 95%. On the other hand, it has allowed railway companies to considerably reduce the costs associated with manual inspections, eliminating a large part of diagnostic errors and speeding up operational decisions. The ability to accurately estimate the depth of contamination has facilitated a more strategic planning of interventions, reducing interruptions in the railway service and maximizing resource efficiency. In addition, thanks to its modular design and its implementation in a container environment, the system is scalable and adaptable to different operating contexts, providing flexibility for use in multiple locations.
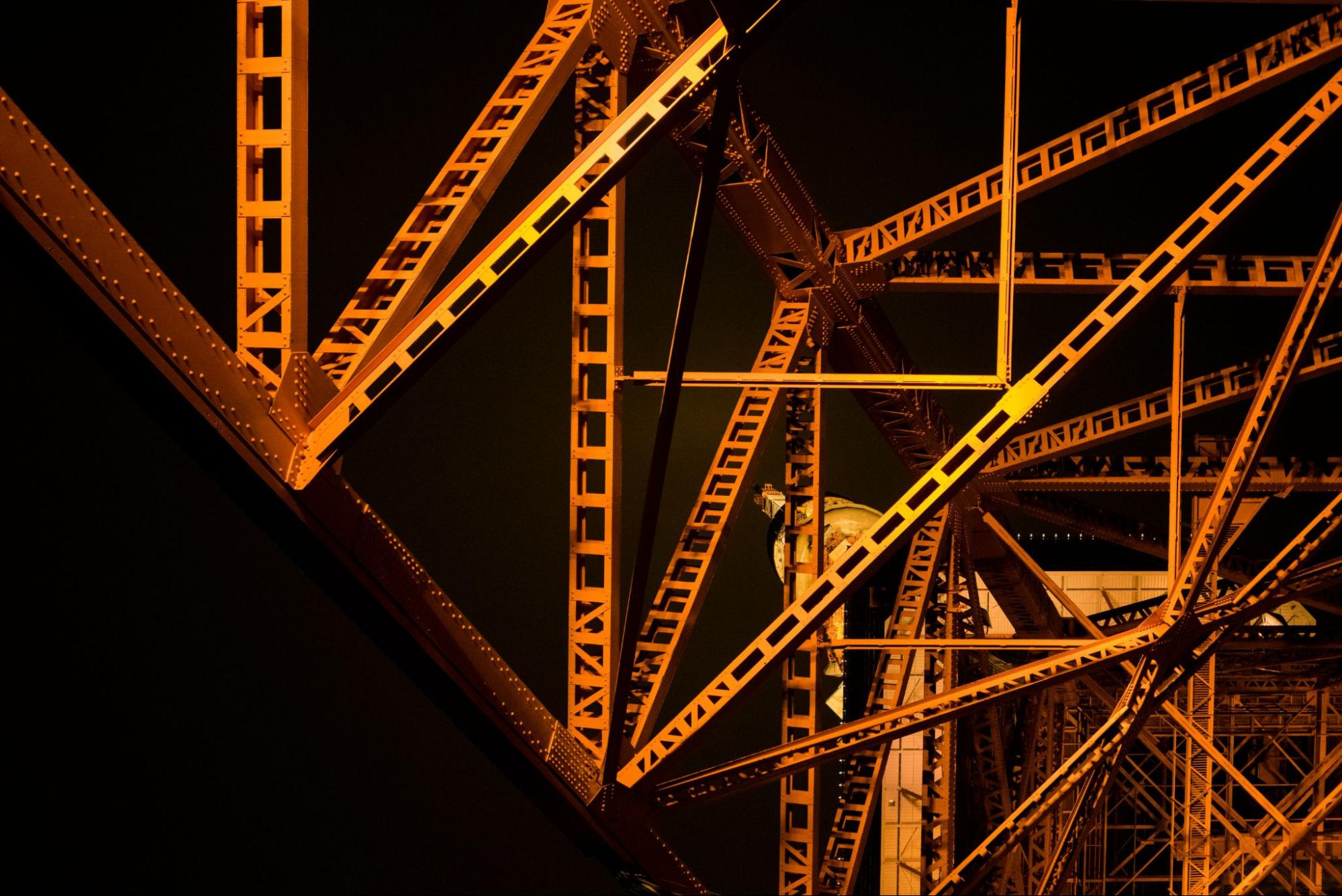
CANETIA
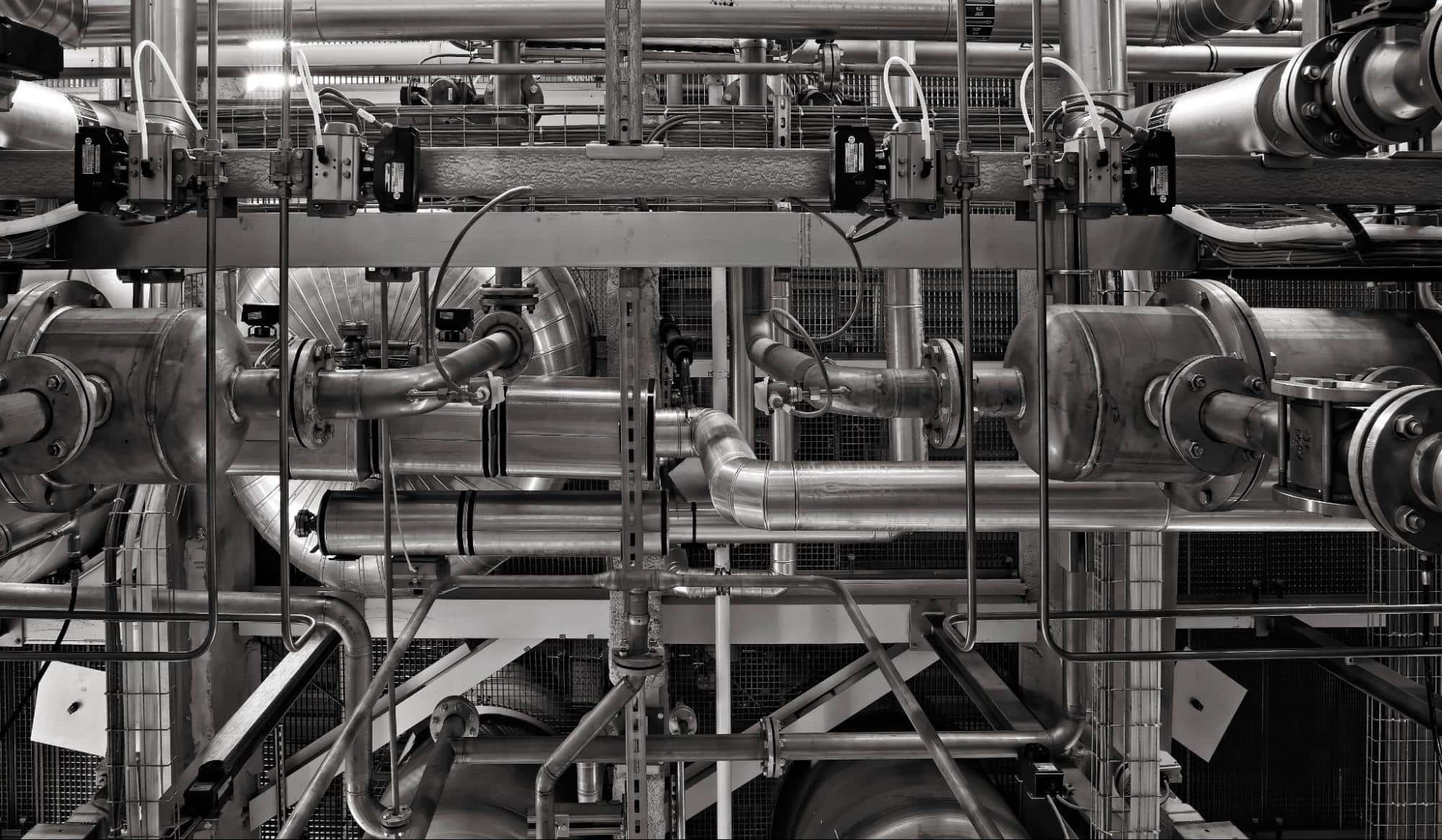
Predictive Maintenance
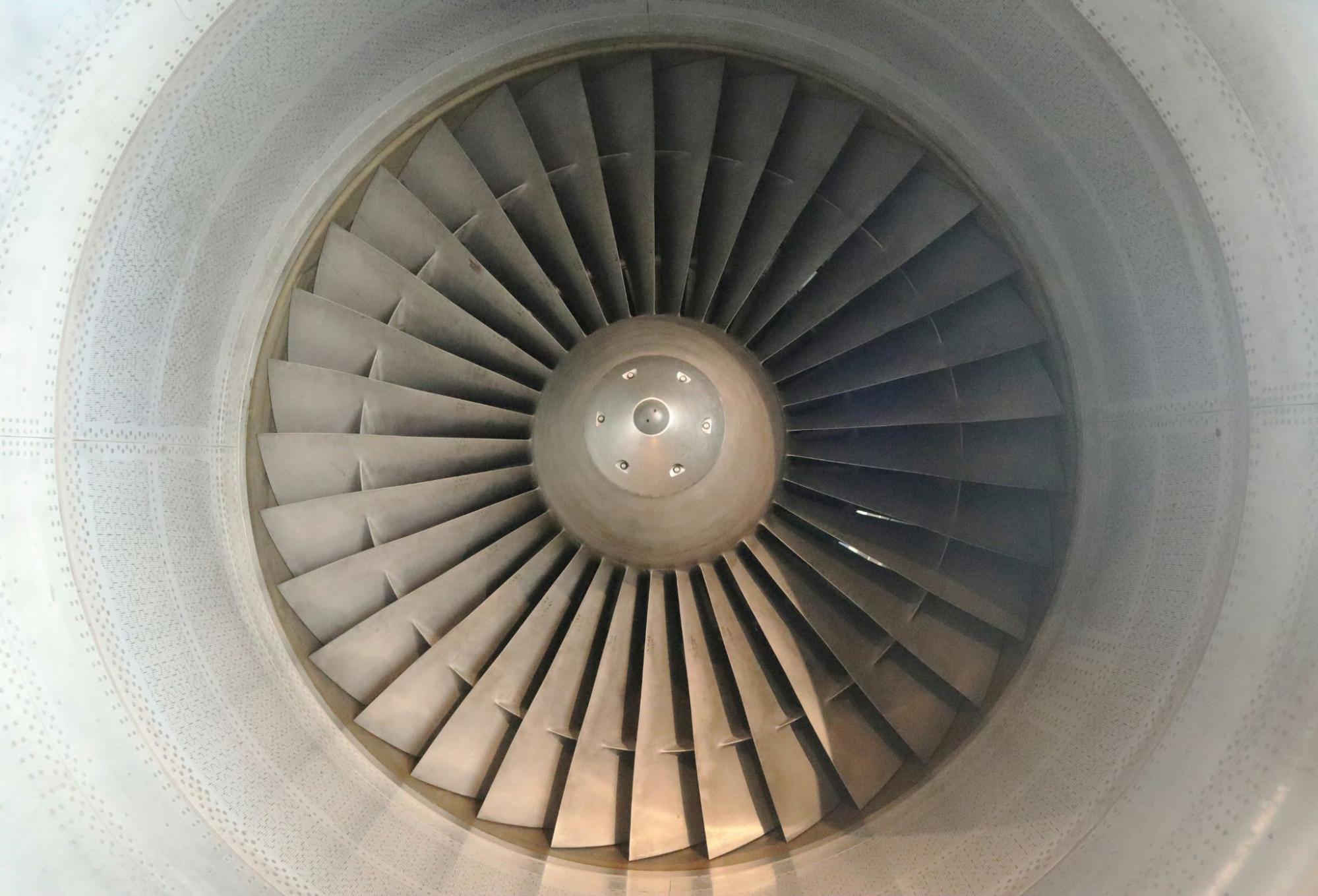