Predictive Maintenance in Gas Turbines
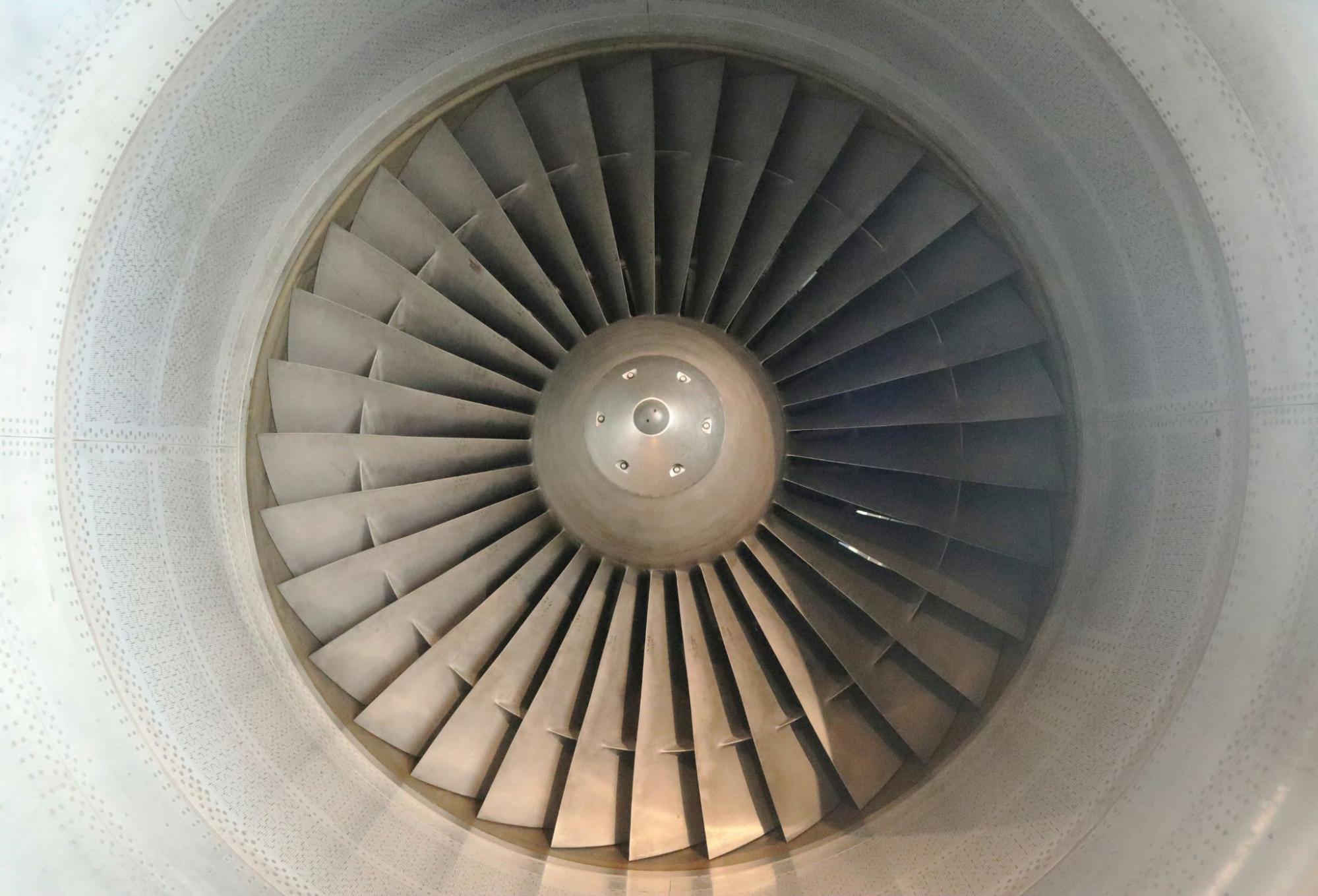
BJ Energy Solutions, a North American company in the oil and gas sector, stands out for its own technology that allows fracking in a more economical and sustainable way, replacing traditional diesel engines with natural gas turbines, which are more efficient and environmentally friendly. These turbines are an integral part of the advanced fracking units called Titan Pumps, equipped with IoT sensors that monitor various operating variables in real time, such as vibrations, temperatures, and pressures. These components are essential but susceptible to failures that can involve million-dollar repairs or even the total loss of units.
At WhiteBox, we started by developing customized ETL processes to consolidate IoT sensor data into a big data infrastructure on Azure, using Synapse Analytics and Delta Lake technology. Next, we created an innovative multivariate anomaly detection model with Spark MLlib, designed to predict catastrophic turbine failures based on their operating conditions. Additionally, we implemented a Power BI tool for the comprehensive visualization of the fleet's status, making it easier for operators to immediately identify any problem and speed up the necessary maintenance. The solution is currently being extended to other parts of the pumping unit besides turbines, such as the "fluid end".
The adoption of the predictive maintenance system has significantly transformed asset management in BJ Energy Solutions, preventing several catastrophic failures and generating multiple savings of around 1 million dollars for each incident prevented. This achievement has not only validated the return on investment in the project, but it has also positioned it as a benchmark for technological innovation in the oil and gas sector, which has historically been very traditional in terms of technological innovation.
- More than 5 TB of processed IoT sensor data.
- More than 50 turbines monitored.
- More than $5 million saved in repairs to date.
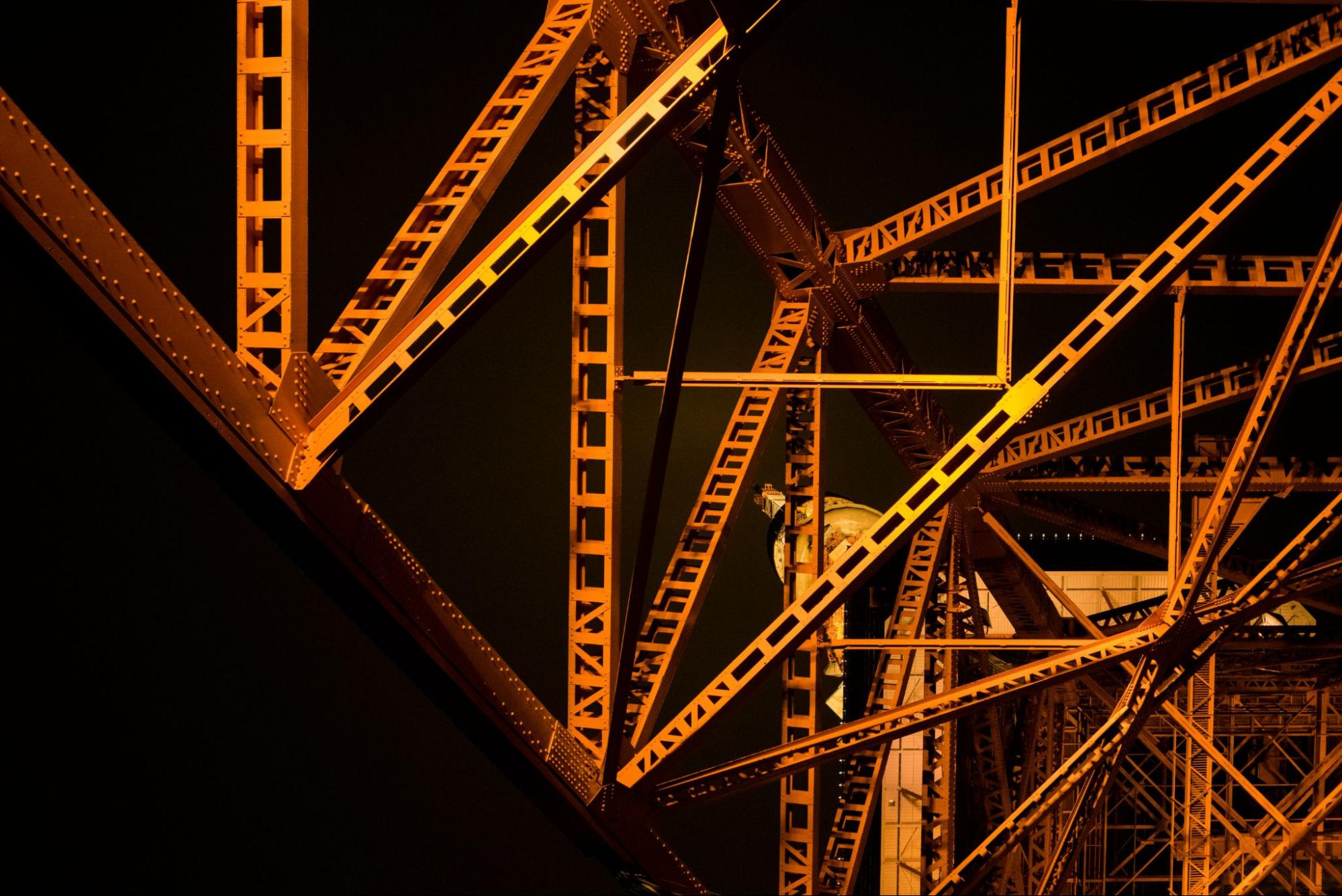
CANETIA
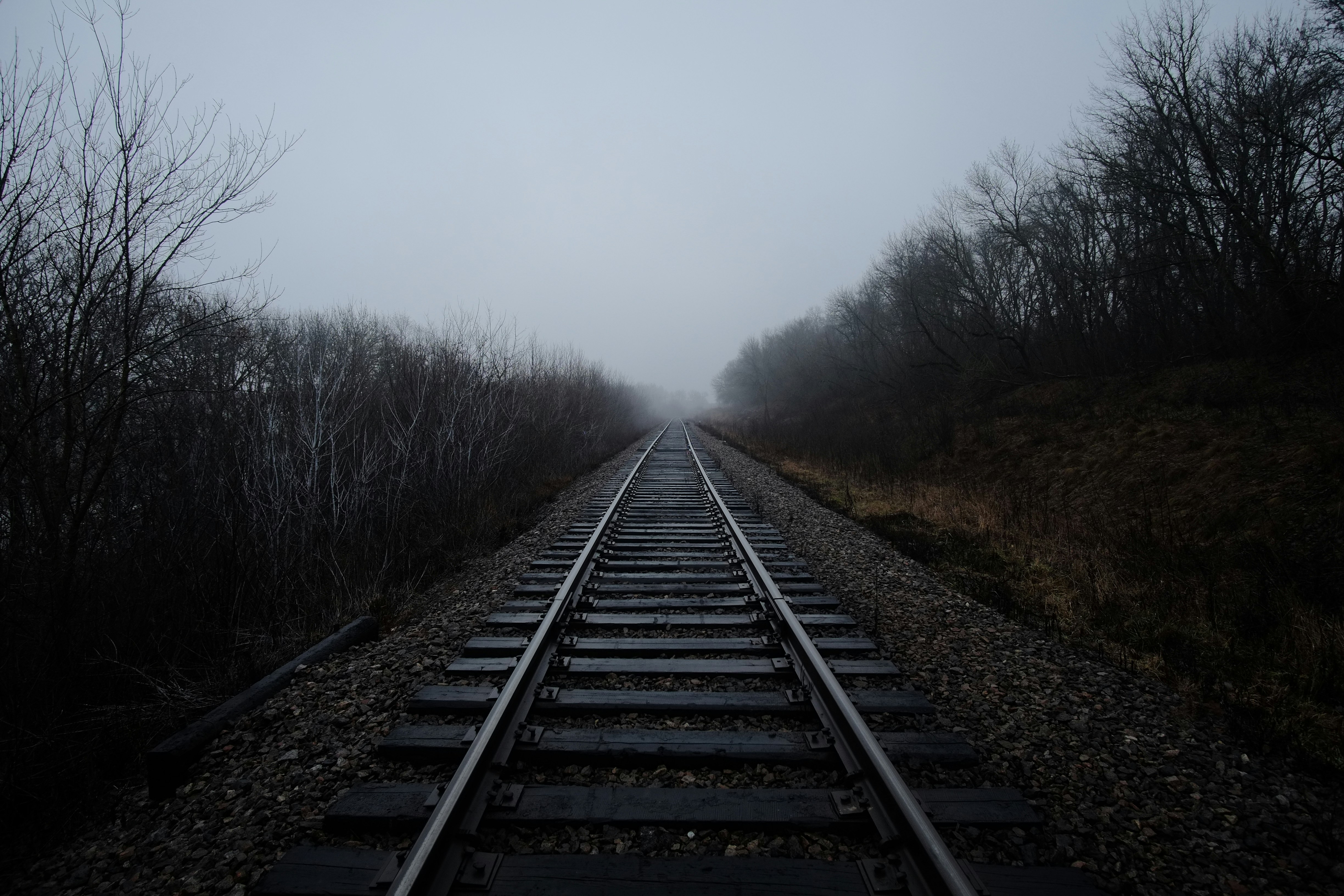